NEWS 035 : INTRODUCING OUR HULL CONSTRUCTION SECTION
In this issue, we introduce our Hull Construction Section, a subdivision of Production Division.
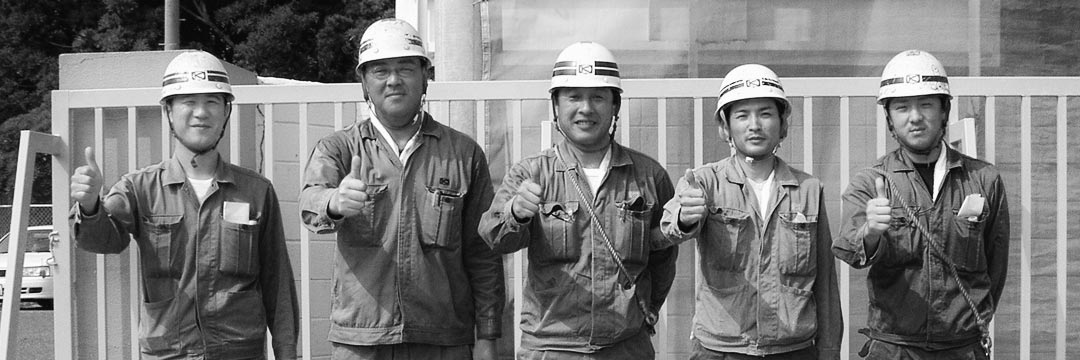
Building of the steel structure of vessels, of which the group is in charge, is at the core of ship manufacturing process. All the shipbuilders are trying hard everyday to implement better management and new technologies in this area, because the total building cost and the process as a whole are largely impacted by how efficiently they can built ship hulls, with minimal influence from weather.
The following are the characteristics of our Hull Construction group, which distinguish Kyokuyo from other companies :
HIGH IN-HOUSE RATIO
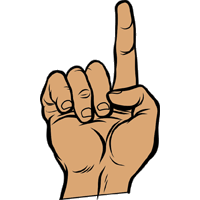
Contrary to other Japanese shipbuilders of our size, we build most of our hull blocks by ourselves. To be more accurate, about 70% of total weight is manufactured in-house, in our all-weather block factory.
Usually, a shipbuilder prefers outsourcing block manufacturing, which do not directly contribute to sales, for reason of economy : one may minimize investment, or save indirect costs incurred by additional manpower this way.
But at Kyokuyo, we have chosen the other way, focusing always on the quality of products. Since most of our blocks are built in-house, access to manufacturing site is guaranteed to our staff and owner's supervisors, and we can precisely control the whole process. If you are like our existing European customers who care the accessibility and the quality of each block, we are sure you will give us a high mark, just like our clients did exactly!
STATE-OF-THE-ART COMPUTER SYSTEMS
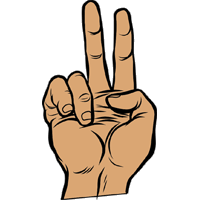
When we built the block factory, we computerized also many of our tasks, including introduction of "SHIP" - a product design system developed by Mitsubishi H.I.- which automated outer shell fairing.
The system, together with NC cutters, has contributed well to improving the degree of precision and shortening building period, as well as remedying working environment.
Now, we are upgrading the system to the newest "NEW SHIP" version, which runs on usual PC's and then enables us to provide a wide array of information on site.
We look forward to having this new tool, which is going to operate in full scale this autumn. It will further enhance our productivity, in combination with our factories.
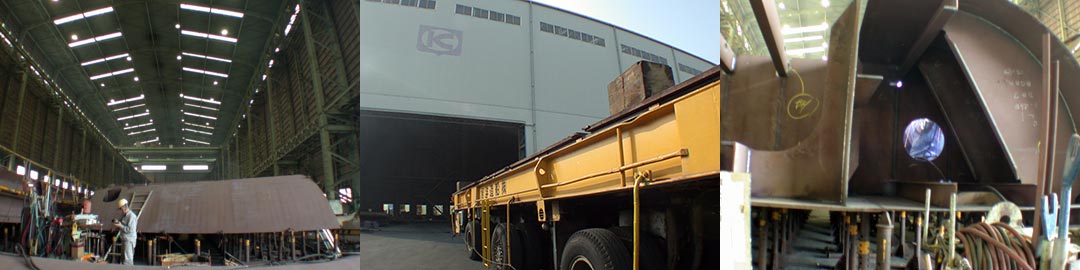
GOOD SKILLS OF LANGUAGE AND COMMUNICATION
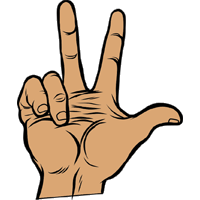
For Kyokuyo, which receives more than 90% of the orders from abroad, it is company's policy and challenge to ensure each of us - from workers to management - has good language skills and communication abilities. We know "quick response on site" is an important factor to eliminate wasting time and to build trust with customer's superintendents.
To further improve our strength, Kyokuyo appointed this year a language school for employees education, and installed 2 sets of AV distance education equipment which enable 2-way remote sessions on real-time basis. With this equipment, our employees can attend lessons in their off-time in near future.
NEW PAINT FACTORY

The most difficult aspect in the process management is dealing with weather. Often rainy and humid, Japan is not always an ideal place for painting a ship. Long rain, or continual high humidity over 80%, which prevents paint from drying, can easily affect the manufacturing process, especially building-up operation in dock.
To put an end to the struggle with weather, we are planning to build a paint factory, which will be equipped with powerful dehumidifiers and efficient sandblasting equipment. Not only allowing us to precisely control the building schedule, this new factory will surely give our customers a great sense of security.
We continue to advance and extend our capabilities, further strengthening our ability to manufacture vessels of superior quality.
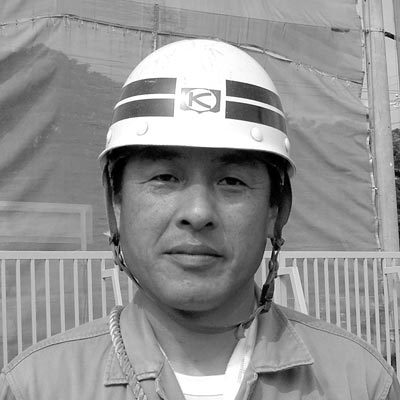
And finally, some words from Satoshi Saeki, 45, who leads the section since this April : "With an average age of 34, my team is young, powerful, and energetic, and making a united effort to further improving our management of safety, manufacturing process and product quality. At the same time, as manager, I focus on maintaining the good flow of communication, within our team and with our customers, including of course their supervisors staying at Kyokuyo. We'll do our best!"
[2004/08/04]